红外压片模具在药品、化工等领域广泛应用,用于将粉末材料压制成片状产品。模具卡死是生产过程中常见的故障之一,不仅影响生产效率,还可能导致设备损坏。为避免这一问题的发生,可以采取一些技巧和预防措施。
一、模具设计优化
1.合理设计模具间隙:在红外压片模具设计时,应确保模具间隙合理。过紧的间隙可能导致粉末材料无法顺畅流动,增加卡死的风险。因此,要根据物料特性来选择合适的间隙,以确保压片过程的顺利进行。
2.采用自清洁设计:一些先进的模具设计采用了自清洁功能,如设置刮刀或定期清洁功能,可以有效减少粉末堆积和粘附的情况,从而减少卡死的可能性。
二、粉末特性控制
1.控制粉末湿度:粉末材料的湿度过高容易导致压制过程中发生粘连或堵塞,进而引起模具卡死。因此,需控制粉末的湿度,确保其在最佳范围内。湿度过高时,可以通过干燥处理来降低湿度。
2.均匀混合粉末:粉末混合不均匀可能导致某些部位的粉末密度过大,从而引发卡死问题。确保原料充分混合,避免颗粒过大或过小的物料堆积,有助于提升模具的运行稳定性。
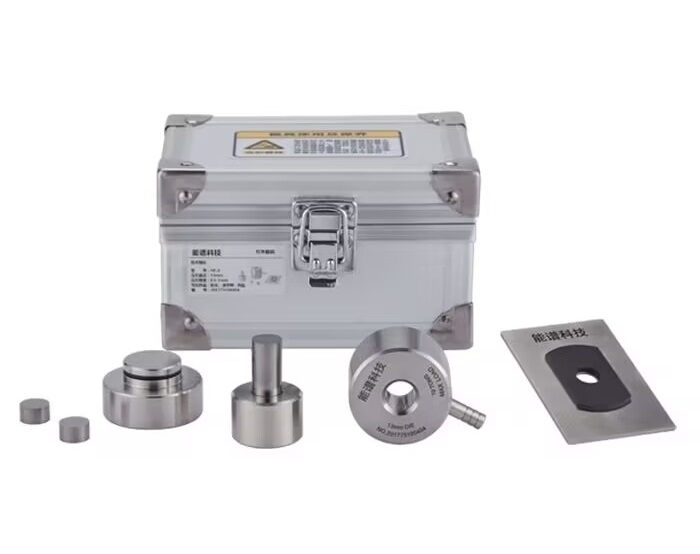
三、设备保养和清洁
1.定期清洁模具:在长时间使用过程中,模具内容易积累粉末残留物或其他杂质。定期进行模具清洁,保持其表面的光滑性,可以有效减少卡死的风险。建议使用专业的清洁工具,避免用过硬的物质刮擦模具表面。
2.润滑系统检查:模具的润滑系统需要定期检查,确保润滑油的质量和量充足。良好的润滑可以减少摩擦力,降低模具卡死的几率。同时,避免润滑油污染物的进入,以免影响模具的正常运转。
四、操作过程的控制
1.均匀加料:加料过程中,要确保加料均匀,避免局部压制压力过大,造成卡死。可以采用振动装置或自动加料系统来实现均匀加料。
2.适当控制压力和速度:压片过程中的压力和速度应根据物料特性进行合理调节。过高的压力或过快的速度都可能导致模具卡死。使用适合的压制参数,确保每一周期的操作平稳顺利。
五、及时故障排查
一旦发现模具卡死的迹象,应及时停机排查原因。通过观察模具和机器的工作状态,可以判断是否因过高压力、粉末湿度不当或润滑不良等因素导致卡死,从而进行针对性调整。
避免红外压片模具卡死问题,关键在于从设计、材料、操作和保养等方面进行综合预防。通过优化模具设计、控制粉末特性、加强设备保养、合理控制操作过程,可以显著降低卡死的发生率,确保生产的高效性与稳定性。